Un escenario complicado, pero ya conocido
Desgraciadamente nos enfrentamos a un nuevo período de crisis en la economía. Ya estamos inmersos en una inflación elevada que no recordábamos desde los años 70, donde la economía se vio alterada por la crisis del petróleo.
Ahora, en el año 2022, nos vemos en una situación parecida motivada por la combinación de la pandemia y las restricciones energéticas derivadas de la guerra de Ucrania.
Vuelve la escasez de recursos y la consecuente subida de precios de dichos recursos.
Las materias primas, los combustibles, la mano de obra… todos los recursos necesarios para el proceso de fabricación elevan sus precios generando un incremento de los costes productivos y obligando a las empresas a enfrentarse a una decisión compleja.
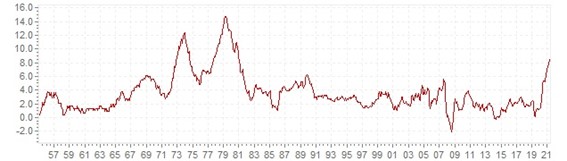
Una decisión difícil de tomar
¿Debo subir los precios de mis productos? ¿Cuánto debo subirlos?
Si para mantener el margen de la empresa, subimos los precios de venta, lo que puede ocurrir es que dejemos de ser competitivos, perdiendo cuota de mercado. Nuestro margen será similar, pero podremos motivar un descenso en el volumen de las ventas que afectaría a la rentabilidad de la empresa.
Por otro lado, si los precios no se actualizan y suben los costes productivos, desciende el margen y descienden los beneficios en la empresa. Si esta situación se alarga en el tiempo la permanencia de la empresa en el mercado también correrá peligro.
La opción habitual suele ser subir los precios, pero no demasiado, para evitar que nuestra competencia se lleve a nuestros clientes.
Esta decisión es más compleja cuando la empresa desconoce sus costes y cómo una variación de los mismos influye en el margen final.
¿Hay algo que se pueda hacer?
No existe una solución sencilla, pero hay pasos que se pueden dar en la dirección de intentar que el impacto sea lo menor posible.
De hecho, si conseguimos reducir la utilización de nuestros recursos productivos, aunque éstos hayan aumentado su precio, el impacto sobre los costes de producción será menor, consiguiendo que el margen no caiga de forma tan abrupta.
Afortunadamente esta situación no es la primera vez que se da. De hecho, en el pasado ya se supo resolver. Lo hizo Toyota con su Toyota Production System, en los años 70. Cambió la forma en la que se fabricaba y sentó las bases de lo que más tarde se llamaría Lean Manufacturing.
Lean Manufacturing
Esta filosofía productiva regresa con fuerza cada vez que se produce una crisis.
Gracias a Lean Manufacturing sabemos que nuestros recursos productivos se invierten en 2 tipos de actividades: actividades con y sin valor añadido, denominadas también como desperdicios o despilfarros.
Actividades con valor añadido. Se trata de actividades que consumen recursos pero que son necesarias para aportar valor al cliente. Son ejemplos de estos tipos de actividad: lijar una superficie, hacer un agujero donde se ensamblará un elemento, hornear un azulejo o colocar el vidrio en una ventana….
Actividades sin valor añadido (desperdicios o despilfarros). También son actividades que utilizan recursos, pero el cliente no las valora y no está dispuesto a pagar por ellas. Son ejemplos de desperdicios: corregir un error de fabricación, transportar producto entre máquinas, almacenar materiales, esperar a que una máquina realice un mecanizado, etc.
Los 8 desperdicios
Inicialmente se consideraron 7 tipos de desperdicios, aunque ya se asume un octavo, que es la infrautilización del talento. Los explicamos a continuación.
Desperdicio por Transporte
Desperdicio proveniente del uso de recursos necesarios para mover materiales desde un punto a otro, dentro y/o fuera de la empresa. Se trata de un desperdicio que nunca se podrá eliminar completamente pero, si se analizan los transportes y las operaciones realizadas en cada punto de la empresa (o fuera de ella), se podrá reducir su impacto.
Desperdicio por Sobreproducción
Este desperdicio se genera al producir más de lo requerido o antes de lo requerido, tanto para el cliente externo como interno. Para evitarlo al máximo debe vigilarse continuamente que el ritmo de producción está en consonancia con la demanda. De hecho, producir cuando no hace falta puede ser más nocivo que permanecer parado. Recordemos las huelgas «a la japonesa».
Desperdicio por Sobreprocesos
Se produce al emplear más recursos de los estrictamente necesarios para realizar una operación. Generalmente se origina cuando los métodos de trabajo no son los más adecuados. Ocasiona un uso de los recursos poco eficiente que desemboca en mayores costes.
Desperdicio por Retrabajos
La mala ejecución de los trabajos repercute en productos defectuosos y una mala imagen de cara al cliente. El desperdicio por retrabajos incluye los recursos invertidos en corregir problemas de calidad que nunca debieron producirse. Este desperdicio va más allá del tiempo desaprovechado cuando, además, se genera producto defectuoso que debe ser saldado o destruido.
Desperdicio por Esperas
Siempre que existen recursos esperando a otros recursos se genera este tipo de desperdicio. Como ejemplos tenemos: operarios esperando a que paren las máquinas, máquinas esperando a que los operarios las pongan en marcha, operarios esperando instrucciones, etc. Además del incremento de costes por la infrautilización de los recursos, se produce un peor nivel de servicio, ocasionado por un alargamiento de plazos innecesario.
Desperdicio por Stock
El desperdicio de stock es un inventario excesivo de cualquier material: materia prima, material auxiliar, repuestos, producto en curso, producto acabado, etc. Las razones por las que se produce son muy variadas: falta de conocimiento de la demanda, aprovechamiento de promociones, etc. Todo el material que tenemos inmovilizado supone un coste para la empresa (lo saben bien los financieros). El gran problema añadido de este desperdicio es que puede enmascarar otros problemas más graves en la organización, como la poca fiabilidad de proveedores o procesos internos.
Desperdicio por Movimientos innecesarios
Se trata de un desperdicio asociado a todos los movimientos que no son estrictamente necesarios para realizar la operación. Su origen suele ser un mal diseño del puesto de trabajo o una falta de organización. Una productividad baja, problemas de calidad y riesgos de seguridad suelen acompañar a este tipo de desperdicio.
Desperdicio por Talento infrautilizado
Las personas son el recurso más preciado en las organizaciones. El desperdicio por talento infrautilizado está vinculado a no aprovechar al máximo las capacidades de las personas de la organización. La falta de formación, supervisión y/o motivación generan graves problemas en la empresa y son fuente de costes importantes.
El impacto de la reducción de los desperdicios en el margen
La implantación Lean permite identificar y reducir progresivamente los distintos desperdicios. El mejor aprovechamiento de los recursos repercute en una mejora también progresiva en el margen de la empresa. Y dicha mejora es, en esencia, la base del incremento de la competitividad de la organización.
En el esquema siguiente se muestra las distintas situaciones en los que se podría encontrar una empresa en relación con la existencia de una crisis y el planteamiento para salir de la misma.
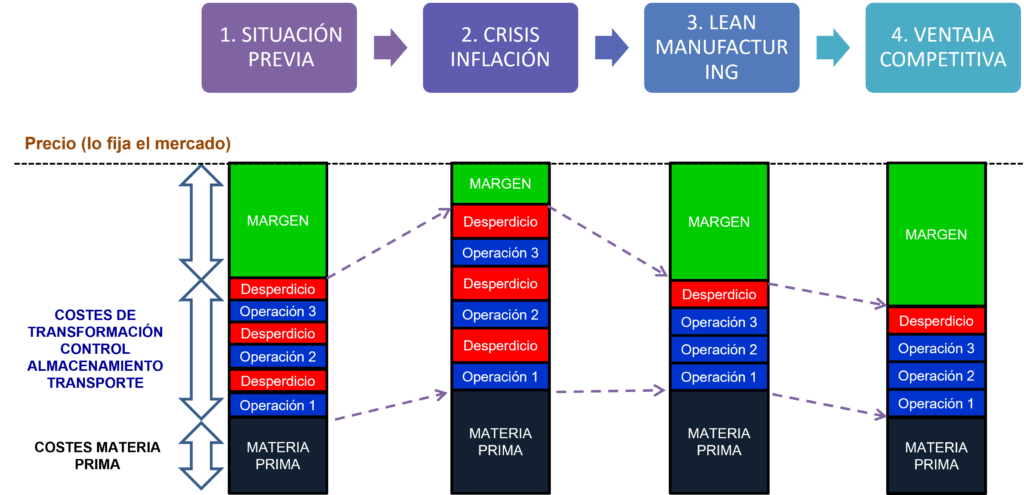
Partimos de la premisa de que el precio lo fija el mercado, por lo que nuestras posibilidades de mejorar el margen quedarán supeditadas a lo que podamos reducir los costes.
1.- SITUACIÓN PREVIA. Se trata de la situación previa a la crisis. En el contexto actual podríamos hablar de cómo estaban funcionando las empresas antes de la pandemia y la guerra de Ucrania. La situación era de crecimiento económico y de buenas expectativas. En este contexto era lógico que las empresas estuviesen más enfocadas en seguir creciendo que en optimizar sus procesos internos.
En el gráfico se muestra un esquema simplificado de los costes y del margen. Se han dibujado los costes de materia prima y los costes de productivos, separando los costes necesarios para crear valor (azul) y los desperdicios (rojo). También se puede ver en color verde el margen restante.
2.- CRISIS E INFLACIÓN. Sobreviene la pandemia y la guerra en Ucrania. Es la situación actual en la que ya se ha producido una escasez de recursos y una subida de precios generalizada, abocándonos a un escenario de inflación.
Esta circunstancia se ha simbolizado en el gráfico con una altura mayor en cada uno de los costes (tanto los costes de materias primas como los de producción). En las flechas discontinuas se ha representado el incremento de costes. También se aprecia la disminución del margen.
3.- LEAN MANUFACTURING. Las amenazas exteriores a la empresa dejan poco margen de maniobra. Si el camino elegido por la organización es buscar la rentabilidad desde dentro, la apuesta por Lean Manufacturing permitirá la optimización de los recursos, reduciendo los costes de producción. Lógicamente este proceso de transformación lleva su tiempo, pero los resultados acabarán llegando tarde o temprano.
En el esquema se muestra una reducción de los costes como consecuencia de la eliminación de parte de los desperdicios (rojo). El margen puede comenzar su lento ascenso. Posiblemente en esta fase ya sea posible comenzar a mejorar los beneficios de la empresa.
4.- VENTAJA COMPETITIVA. Pero el proceso de mejora no tiene porque finalizar aquí. Si la apuesta por el cambio del modelo productivo se mantiene en el tiempo, será posible mantener la mejora interna que provocó la implantación de Lean Manufacturing. Los costes de las materias primas volverán a bajar con el tiempo y la consecuencia será un margen adicional con el que la empresa nunca contó en el pasado. Ésta se podría convertir en una ventaja competitiva para la empresa que le permita destacar respecto de su competencia.
Gráficamente esta situación se representa con el descenso de los costes de las materias primas y el consecuente incremento del margen, superior incluso al que se tenía en el primer escenario.
Conclusiones
Lean Manufacturing no es la panacea. Requiere visión de futuro, rodearse del personal adecuado y trabajar mucho para hacer las cosas bien desde dentro de la empresa. Y no hay que engañarse, en función del punto de partida, puede que sea muy difícil revertir la situación. Lo que sí se puede afirmar con rotundidad es que marca un camino a seguir, lleno de esfuerzo y sacrificio, pero que permite vislumbrar una luz al final del túnel.
Conozca más sobre nosotros y cómo podemos ayudarle en GEMBA LEAN CONSULTING