¿Cómo están funcionando nuestras líneas de producción? ¿Qué deberíamos hacer para que fuesen más rentables? ¿Quién lo debe hacer, los operarios, los encargados, el equipo directivo?…
Para responder a todas estas preguntas debemos empezar entendiendo cómo funcionan nuestras líneas y para eso necesitamos medir, porque “Todo lo que se mide, mejora”, según pronostica una máxima de Calidad.
OEE, Productividad y Tasa de Defectos
Los KPI (Key Performance Indicators) o “Indicadores clave de rendimiento” son métricas que permiten controlar el correcto funcionamiento de los procesos, en nuestro caso, las líneas de producción.
Si medimos los KPIs de nuestras líneas de producción, podremos conocerlos con detalle e iniciar un proceso de mejora orientado a elevar la rentabilidad de los mismos.
Existen 3 KPIs imprescindibles para las líneas de producción, la eficiencia, la productividad y la tasa de defectos.
EFICIENCIA
El primer Indicador clave que debemos conocer es la eficiencia.
La eficiencia de un proceso (o de una máquina) es la relación que existe entre la producción real obtenida y la producción máxima teórica.
Por ejemplo. Supongamos que una máquina puede producir teóricamente 1.000 unidades/hora. Durante 8 horas, debería haber producido 8.000 unidades. Sin embargo, al final del día, comprobamos su producción real y ha sido de 4.800 unidades. La eficiencia de la máquina ha sido de 4.800/8.000 = 60%.
Una eficiencia del 60% nos dice que estamos aprovechando nuestra máquina en ese porcentaje. O lo que es lo mismo, la eficiencia mide el aprovechamiento de la instalación.
Una empresa será tanto más competitiva cuanto mayor sea la eficiencia de sus procesos.
Pero…¿qué ha pasado con el 40% restante? Se ha transformado en lo que se denominan “pérdidas”.
Las pérdidas del proceso son todo aquello que impide que la eficiencia sea del 100% y se clasifican en 3 grandes grupos:
- Pérdidas por Disponibilidad. Aparecen siempre que se produce una parada de la máquina (averías, cambio de formato, falta de material, falta de personal, arranque de máquina, etc.).
- Pérdidas por Rendimiento. Se producen cuando la máquina no ha parado, pero fabrica a una velocidad inferior a la teórica. Las pérdidas por rendimiento pueden ser de 2 tipos: las pérdidas por microparadas (paradas de muy poca duración, pero muy frecuentes) y las pérdidas por velocidad reducida, debidas a disminuciones voluntarias de velocidad, ocasionadas por problemas de calidad, inicios de fabricación, etc.).
- Pérdidas por Calidad. Este tipo de pérdidas se producen al utilizar la instalación para fabricar un producto no conforme. El tiempo empleado en procesar un producto que no cumple con la especificación es tiempo irrecuperable, que dará lugar a las pérdidas de calidad. En este grupo también se incluyen las pérdidas derivadas de reprocesar productos.
El OEE (Overall Equipment Effectiveness) o Eficiencia Global de los Equipos, en el indicador que permite medir la eficiencia con la que trabaja un equipo o un proceso.
Se trata de un indicador universal, conocido a nivel mundial y utilizado por todo tipo de empresas, en todos los sectores.
El OEE se puede entender cómo la relación que existe entre el tiempo que teóricamente debería haber costado fabricar las unidades correctas obtenidas (si no se hubiesen producido paradas, a la máxima velocidad y sin unidades defectuosas) y el tiempo que realmente ha costado.
Desglosaremos esta información utilizando la gráfica adjunta, en la que se muestran los distintos tiempos y tipos de pérdidas. Según dicha gráfica:
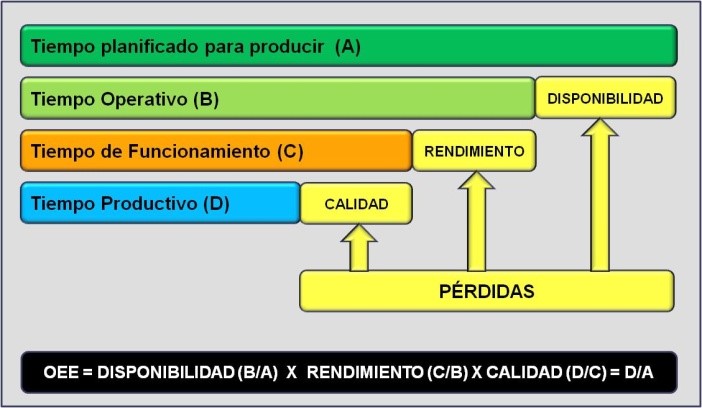
El OEE se puede descomponer en el producto de 3 factores, relacionados a su vez, con los 3 grandes grupos de pérdidas. Son las llamadas Tasas de Disponibilidad, Rendimiento y Calidad.
OEE = Tasa Disponibilidad x Tasa Rendimiento x Tasa Calidad
El OEE y las pérdidas nos permiten realizar un análisis pormenorizado de las oportunidades de mejora que podemos encontrar en nuestras líneas de producción.
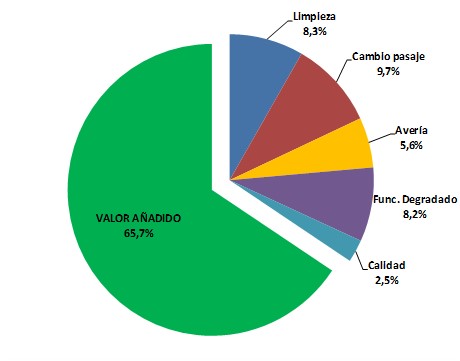
PRODUCTIVIDAD
El segundo indicador clave que debemos conocer es la productividad.
La productividad de un proceso es la relación que existe entre la producción real obtenida y los recursos empleados para conseguirla.
Productividad = Cantidad fabricada/Recursos empleados
La productividad mide el aprovechamiento de los recursos humanos utilizados en el proceso.
En nuestro ejemplo anterior, supongamos que, para producir 4.800 unidades, hemos necesitado a 2 personas trabajando durante 1 turno de trabajo, siendo el turno de 8 horas.
Productividad = 4800 uds. /(2 personas * 8 horas)
La productividad es de 300 uds/hora-persona.
Al igual que ocurría con el OEE, la empresa será tanto más competitiva cuanto más alta sea su productividad, ya que necesitará menos recursos para obtener la producción deseada.
La productividad nos permite conocer y controlar el consumo de recursos humanos en las líneas de producción, teniendo un impacto muy importante en los costes de producción.
TASA DE DEFECTOS
El tercer KPI es la tasa de defectos.
La tasa de defectos de un proceso es la relación que existe entre la producción no conforme y la producción total realizada.
Tasa de defectos = Cantidad fabricada no conforme/Cantidad fabricada total

La tasa de defectos nos ayuda a determinar la capacidad de nuestros procesos para cumplir con las especificaciones requeridas para el producto.
Una tasa de defectos elevada, afecta de múltiples formas a la rentabilidad del proceso, ya que supone:
- Malgastar tiempo de la máquina en procesar un producto inservible o que deberá ser reprocesado para que sea conforme.
- Malgastar los recursos humanos necesarios para llevar a cabo el proceso o que se utilizarán para reprocesar el producto no conforme.
- En el peor de los casos, cuando el producto conforme no se pueda reprocesar, también se podrá perder el material utilizado, incrementando la merma de producción.
- Además, se producirán gastos adicionales de energía, consumibles, etc.
Por estos motivos, es imprescindible el control de la defectología del proceso, a través de la tasa de defectos.
EL PROCESO DE MEJORA CONTINUA
Pues bien, sólo nos queda saber cómo utilizar estos indicadores para mejorar la rentabilidad de nuestras líneas de producción. Para ello, utilizamos una metodología de Mejora Continua, de carácter cíclico y cuyos pasos se resumen a continuación.
Ciclo de Mejora Continua
Paso 1. Medición de los KPIs (OEE, Productividad y Tasa Defectos) iniciales, para conocer el punto de partida de forma clara y concisa.
Paso 2. Análisis de las causas que impiden que dichos KPIs sean mayores. Será de suma importancia conocer al máximo detalle las pérdidas de la línea de producción (cambios de formato, ausencias de personal, averías, etc.). Una vez cuantificadas dichas pérdidas será sencillo establecer una priorización. Se procederá de idéntico modo con la defectología generada en el proceso productivo.
Paso 3. Elaboración de un Plan de Acción, con responsables y plazos, cuyo cumplimiento asegure mejoras notables en el funcionamiento de la línea y consecuentemente, en la rentabilidad de la misma.
Paso 4. Esta última fase corresponde a la ejecución del Plan de Acción previsto.
Y este proceso se repetirá de forma cíclica e indefinida. Es decir, finalizado el punto 4, volveríamos al punto 1 en el que calcularíamos los nuevos valores de OEE, Productividad y Tasa de defectos, comprobando el impacto de las acciones implantadas. Se realizaría un nuevo análisis de pérdidas y defectos, generando nuevas acciones a incluir en un nuevo plan, que volveríamos a ejecutar.
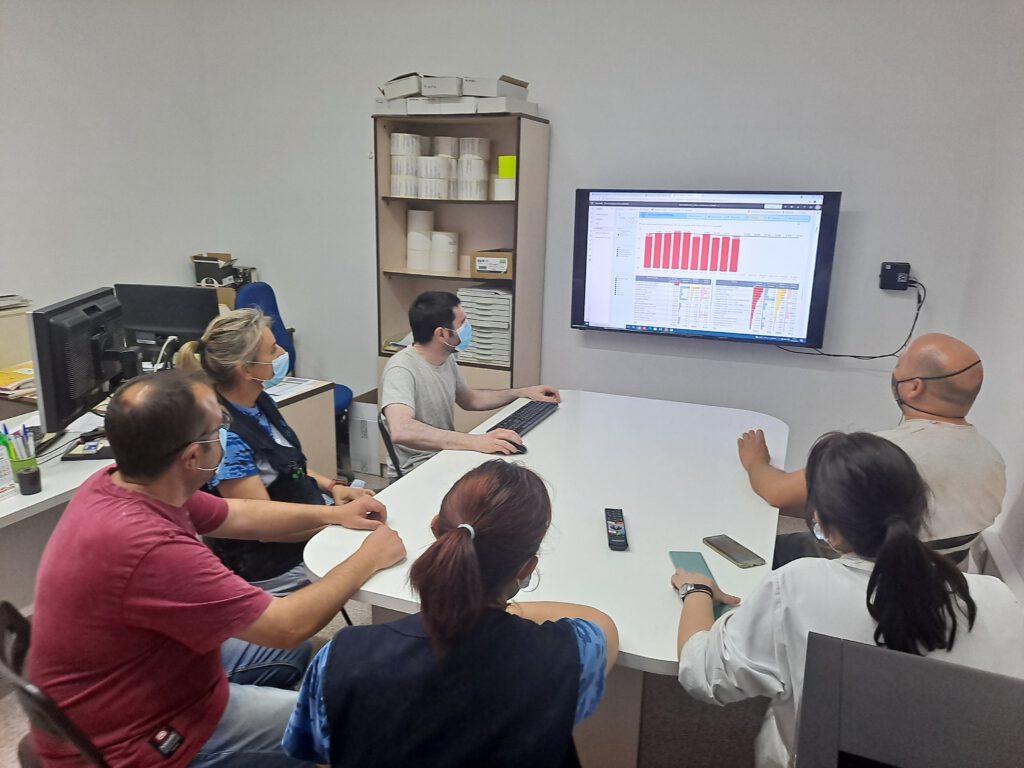
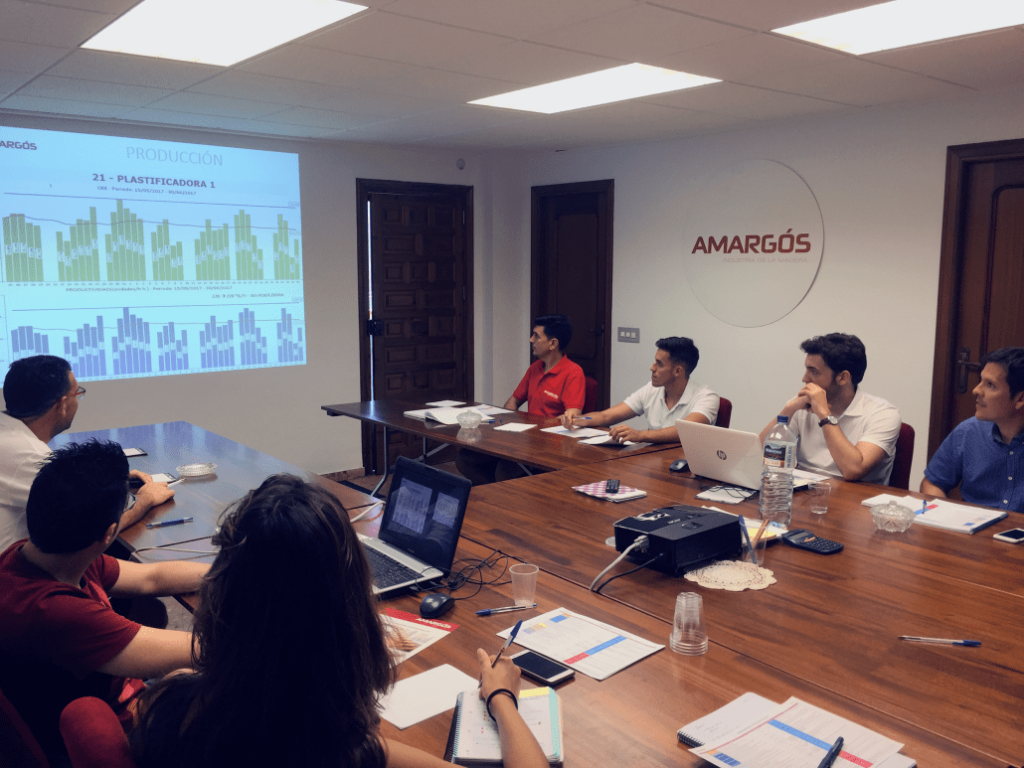
BENEFICIOS
La aplicación de un sistema de medición en las líneas de producción repercute en una serie de beneficios, tales como:
- Rigor en la información. Los KPIs OEE, Productividad y Tasa de defectos, aportan información fiable y objetiva sobre la que trabajar. La gestión de producción ya no se basa en sensaciones, sino en datos y problemas concretos, definidos al detalle y cuantificados.
- Participación e implicación de todo el personal. Esta información de indicadores se traslada a paneles distribuidos por la planta para que todo el personal (operarios, mandos, directivos…) tenga acceso a ella y puedan participar al máximo en la gestión.
- Priorización de acciones enfocada a resultados. Los planes de acción generados, permiten atacar los principales problemas de las líneas de producción. En dichos planes, se conoce previamente una estimación de los resultados que es posible alcanzar y se alinea a personas de distintos departamentos y niveles jerárquicos.
- Se produce un cambio cultural de la empresa hacia la mejora continua. La metodología empleada genera una forma de abordar los problemas más participativa y multidisciplinar. Es habitual la creación de grupos Kaizen para la gestión de la mejora continua.
Todo ello repercute en la mejora sostenible de la rentabilidad de las líneas de producción en el tiempo, dotando a las empresas de una ventaja competitiva, que proviene de hacer las cosas bien desde el interior de la organización.