Qué es el Gemba
Gemba es uno de los conceptos clave de lean manufacturing: gemba (lugar de trabajo), gembutsu (el producto en elaboración) y genjitsu (los hechos).
Cualquiera que quiera conocer cómo y dónde se produce el valor en su organización, debe ir al «gemba», que en el caso de las empresas productivas, es la propia fábrica.
Reglas del paseo Gemba
El «gemba walk» o paseo gemba es la forma en que el mando o el directivo toma contacto con la realidad de la producción, y la comprende en profundidad. Se trata de una pieza clave en el proceso de mejora continua.
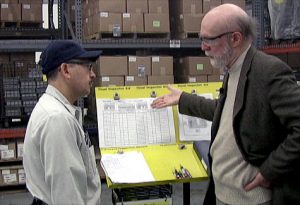
Para que este paseo sea efectivo, deben cumplirse una serie de reglas básicas, que se resumen en la expresión «Go see, Ask why, Show respect» (Jim Womack).
Go see. Ir a ver. Lo primero de todo es ir a ver cómo funciona el proceso. Pero ¿qué es lo que buscamos? Buscamos saber si los procesos y las personas están alineados para conseguir los objetivos de la empresa.
Ask why. Preguntar ¿por qué?. El paseo gemba tiene como objetivo conocer con detalle el proceso e impulsar soluciones a los problemas. Las preguntas ¿qué?¿cuándo?¿cómo? o ¿quién? no incitan a la reflexión por parte del operario. Sin embargo, la pregunta ¿por qué? impulsa a cuestionarse las acciones habituales y activa la creatividad, guiando a la persona a encontrar su propia solución.
Show respect. Respeto por el personal. Cuando se va a iniciar un diálogo con alguna persona en el gemba, debe realizarse con cordialidad y concreción. Hay que comenzar saludando. Las preguntas deben ser cortas y deben estar centradas en el propio gemba. No se trata de socializar, pero sí mostrar nuestro interés sincero por cómo se sienten las personas y averiguar cómo podemos facilitar su correcto desempeño.
¿Qué se tiene en cuenta en el paseo Gemba?
¿Cómo comenzamos un paseo gemba?
No podemos pretender ir al gemba en busca de todo. Podríamos perdernos en multitud de detalles y acabar confundiendo a las personas que allí están. Lo más sencillo es utilizar una especie de guía, fijándonos en aspectos como:
Orden y limpieza
Observamos que en los puestos de trabajo se ha eliminado todo lo que es innecesario. Todos los elementos que sí hacen falta, tienen un lugar definido y conocido por todos. El lugar está limpio y las condiciones de seguridad son las adecuadas. Existe información clara sobre las zonas de trabajo, accesos, pasillos y todo aquello que permita una sencilla gestión visual.
Flujo de materiales
La cantidad de material en curso debe ser la necesaria para el correcto funcionamiento del proceso productivo. Debe prestarse atención a las acumulaciones de material y los motivos por los cuales se han producido. Especialmente importantes son los materiales rechazados o retenidos y los productos obsoletos. La cantidad de material en estanterías, zonas de espera, búferes, etc. debe estar perfectamente definida.
Información en paneles
Los paneles de información deben estar al día y deben reflejar el funcionamiento en las células o líneas de producción. Debe poderse comprobar de forma sencilla, si existen desviaciones entre los indicadores y los objetivos previstos. También es deseable que aparezca la información sobre los planes de acción en curso.
Mantenimiento de los equipos
Se debe comprobar que los estándares de mantenimiento están disponibles y los registros actualizados. Las máquinas están limpias y no hay fugas de aceite, aire o cualquier otro fluido.
Oficinas y resto de áreas en planta
También deben cumplir con unos mínimos de organización, acorde al resto de la planta.Autor: Francisco Espín